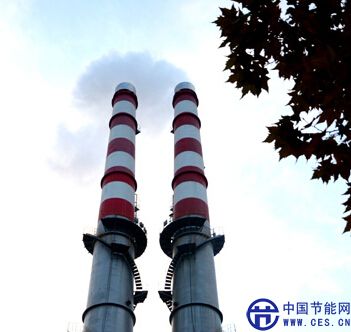
据了解,金陵石化所有热电锅炉烟气的排放都实施了脱硫脱硝双重处理,以投资3.2亿元的代价换来了每年减排6000吨氮氧化物和7000吨二氧化硫的绿色成果,让南京的蓝天白云更加瑰丽。
多年来,金陵石化高度重视环保工作,积极推进绿色发展战略。2008年底,该公司热电4台煤粉炉烟气脱硫装置建成投入运行。经过可研性分析,该公司又着手锅炉脱硝改造的施工。
该公司根据热电生产的安排,分期分批组织了剩余2台锅炉的脱硫和6台锅炉的脱硝改造。2013年4月24日Ⅲ锅炉改造动工,正式拉开了又一轮热电环保改造的序幕。
该公司共有4台煤粉锅炉和2台循环流化床锅炉,不同的锅炉实施的改造技术当然不同。煤粉锅炉的脱硝系统,采用低氮燃烧器以及选择性非催化还原、选择性催化还原相结合的技术,降低烟气中的氮氧化物含量。此技术在国内使用不多,系统相对复杂,调节要求较高。循环流化床锅炉脱硝系统采用选择性非催化还原、选择性催化还原相结合的技术,国内企业应用较少,可借鉴经验不多。
而且锅炉脱硫脱硝项目轮流实施,时间紧、任务重,建设点多、面广,上下交叉作业多。该公司加强项目建设过程监管,细化每道工序,紧盯过程中的每个环节,严把质量关,同时加强直接作业环节监管,做到只要有作业的地方就有安全监管人员,及时进行纠偏,杜绝违章作业,确保安全措施落实到位。6台锅炉脱硫脱硝改造后,均实现了一次开车成功,并且氮氧化物排放浓度降低到100mg/Nm3以下,每年减排氮氧化物6000吨、二氧化硫7000吨,环保效益显著。