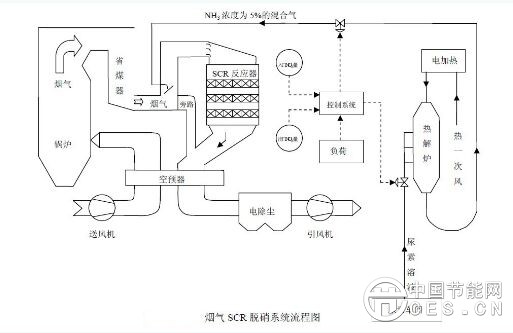
1.1 以氨做还原剂,通常在空气预热器的上游注入含NOX的烟气,此处控制烟气温度在290℃~400℃(催化还原的最佳温度),在含有催化剂的反应器内NOX被还原为N2和H2O,催化剂的活性材料通常由贵金属,碱性金属氧化物和/或沸石等。
1.2 反应原理:
4NH3+4NO+O2→4N2+6H2O
8NH3+6NO2 →7N2+12H2O
与氨有关的潜在氧化反应:
4NH3+5O2 →4NO+6H2O
4NH3+3O2 →4N2+6H2O
1.3 影响SCR脱硝的主要因素
1.3.1 SV值
一般催化剂的数量是用每立方米的催化剂层能处理多少烟气流量来表示,这实际上是一个空间速度SV值。
SV值越大,表示单位体积的催化剂层能处理的烟气量越多。因此,希望SV值越大越好。然而,实际上SV过大会降低催化剂的反应率。
1.3.2 NH3/NOX摩尔比
NH3量不足会导致NOX的脱出率降低,但NH3过量又会产生二次污染,通常喷入的NH3的量随着机组负荷的变化而变化。
1.3.3 烟气温度
烟气温度低时,不仅会因催化剂的活性降低而降低NOX的脱除效率,而且喷入的NH3还会与烟气中的SOX反应生成(NH4)2SO4附着在催化剂表面;烟气温度高时,NH3会与O2反应,导致烟气中的NOX增加。
1.3.4 烟气在反应器内的空间速度
烟气(标准状态下的湿烟气)在催化剂容器内的停留时间尺度,在某种程度上决定反应物是否完全反应,同时也决定着反应器催化剂骨架的冲刷和烟气的沿程阻力。空间速度大,烟气在反应器内的停留时间短,则反应有可能不完全,这样NH3的逃逸量就大,对催化剂骨架的冲刷也大。对于固态排渣炉高灰段布置的SCR反应器,空间速度选择一般是(2500~3500)h-1。
1.3.5 烟气流型及与氨的湍流混合
烟气流型的优劣决定着催化剂的应用效果,合理的烟气流型不仅能较高地利用催化剂,而且能减少烟气的沿程阻力。设计最佳喷氨点,其中湍流条件要实现与烟气的最佳混合,形成明确的均相流动区域。
1.3.6 催化剂钝化
(1)原因:长时间暴露于450℃以上的高温环境中可引起催化剂活性位置(表面积)烧结,导致催化剂颗粒增大,表面积减小,因而使催化剂活性降低。
措施:采用钨退火处理,可最大限度地减少催化剂的烧结。在正常的SCR运行温度下,烧结是可以忽略的。
(2)原因:Na、K腐蚀性混合物如果直接和催化剂表面接触,在催化剂活性位置的碱金属与其他物质发生了反应,从而使催化剂活性降低。
措施:对于大多数应用,避免水蒸气的凝结,可以排除在此类危险。
(3)原因:飞灰中游离的CaO和SO3反应,可吸附在催化剂表面,形成CaSO4,催化剂表面被CaSO4包围,从而使催化剂活性降低。
措施:工艺中脱硝工艺之前应添加有脱硫工艺。
(4)原因:由于铵盐及飞灰中的小颗粒沉积在催化剂小孔中,阻碍NOX、NH3和O2到达催化剂表面,引起催化剂阻塞。
措施:通过调节气流分布,选择合理的催化剂间距和单元空间,并使SCR反应器烟气的温度维持在铵盐沉积温度之上。
(5)原因:由于飞灰撞击在催化剂表面,引起催化剂腐蚀问题。腐蚀强度与气流速度、飞灰特性、撞击角度及催化剂本身特性有关。
措施:采用耐腐蚀催化剂材料,提高边缘硬度;利用计算流体动力学流体模型优化气流分布,在垂直催化剂床层安装气流调节装置。
1.3.7 SO2对SCR反应的影响
烟气中SO2会在催化剂的作用下被氧化成SO3,SO3与烟气中的水及NH3反应,从而生成(NH4)2SO4和(NH4)HSO4。这些硫酸盐可以沉积并集聚在催化剂表面,阻碍催化剂进一步催化反应。