易门铜业有限公司ZO—6500型VPSA制氧系统的一台罗茨鼓风机,风机型号为ARG500,转速为742r/min,排气压力49KPa。该风机最高振动值从2009年4月15日起开始逐渐变大,由表1可看出,水平振动速度有效值超出了15mm/s的允许范围,垂直振动速度有效值也有所上升。造成系统多次联锁停机,严重影响了风机安全运行。由于该制氧系统使用的风机出口压力每隔24s都要完成一个从31—41KPa加压过程,风机的出口压力波动频繁,振动值随压力也相应发生变化。给分析和查找振动原因带来了一定困难。为此,对罗茨鼓风机振动进行了全面的测试和分析,找出了故障原因,并进行了处理,保证了罗茨鼓风机的安全运行。
1罗茨鼓风机振动原因分析及特征
引起罗茨鼓风机振动大的因素较多,主要原因有以下几种:
1.1地脚螺栓松动,主要表现在垂直方向振动较大。
1.2联轴器找正不合格,表现有三点:一是轴向振动较大,二是与联轴器靠近的轴承振动较大,三是振动程度与负荷关系较大。
1.3风机基础刚度差,故障特征为:一是振动频率为工频,振动时域波形为正弦波,二是垂直方向振动速度异常。
1.4与风机连接的管道配置不合理,主要是与风机连接的防振接头老化,管道与风机形成共振。
1.5同步齿轮啮合间隙大,齿面接触精度不够,也可导致水平振动超标。
1.6转子不平衡,振动表现为:一是水平方向振动较大,且振动频率与转速同频,二是振动大小与机组负荷无关。
1.7轴承损坏及轴系零件松动,主要表现在:一是轴承温度高并有异响,二是水平、轴向、垂直振动都有异常。
2故障查找
对照以上分析情况,分别对风机地脚螺栓、联轴器、风机基础及与风机连接的管道进行了检查,未发现异常。并且在2007年因振动大对风机基础进行过重新加固浇灌,因此也可以排除风机基础刚度差的原因。轴承温度无变化以及未发现异常声音。
为查清原因,5月3日用振通908简易测振仪对风机水平、垂直、轴向振动进行测量,风机出口压力在31—41KPa运行时结果如表2,由测量结果可看出,后轴承端比前轴承端振动值大3mm/s左右,说明振动是从后轴承端引起。为检查是否存在转子动不平衡,对风机出口压力下降到21--34KPa和升到35—45KPa分别进行了测量,振动值无明显变化。因此可以肯定,风机转子不存在动不平衡,振动源出在风机后端,可能是轴承及轴系零件松动造成。
风机后端装配有同步齿轮、轴承、调整垫及轴承定位衬套,为排除故障,决定对风机后端拆开检查,发现同步齿轮啮合良好,齿面处于磨合状态,无明显磨损现象,初步排除了齿面接触精度不够原因。拆除同步齿轮后,发现两个转子的轴承锁紧螺母非常松,轴承明显跑内圈,拆下轴承后测量轴已磨损0.5mm。并且轴承定位衬套的定位销掉,衬套处轴也磨损严重。产生振动的原因可以确定,与以上分析相啮合,由于轴承锁紧螺母松动,造成轴承跑内圈,轴承定位衬套出现相对运动,导致转子径向间隙及同步齿轮啮合间隙大,振动值增大。
3故障处理
ARG500罗茨鼓风机叶轮与轴采用热装,无法更换轴,而购买一套转子费用较高,时间较长,是生产经营所不允许的。经分析研究决定对轴进行修复,为防止转子产生弯曲变形,以及表面粗糙度达到要求,采用激光熔覆新技术和表面喷镀方法。
3.1激光熔覆技术的原理及特点
激光熔覆,通常采用预置涂层或喷吹送粉的方法加入熔铸金属,利用激光束聚焦能量极高的特点,在瞬间将基体表面仅微熔。同时使基体表面预置的熔覆层金属粉末(与基体材料相同或相近)全部熔化。当激光离出后快速凝固,获得与基体冶金结合的致密覆层。从而达到使零件表面恢复几何尺寸和表面涂层强化的作用。
激光熔覆技术可以解决手工电弧焊、氩弧焊、喷涂、镀层等传统修复方法无法解决的材料选用局限性、工艺过程热应力、热变形、材料晶粒粗大、基体材料结合强度难以保证等问题。激光熔覆层与基体为冶金结合,结合强度不低于原基体材料的90%,基体材料在激光加工过程中仅表面微熔,微熔层为0.05~0.1mm,基体热影响区一般为0.1~0.2mm,温升不超过80℃,激光加工后无热变形。且覆层组织致密,晶体小、无孔洞、无夹渣裂纹等缺陷。
3.2修复过程
修复工作委托昆钢联合激光公司进行,利用一台2KW的激光机,对所需修复部位进行手工熔覆修复。在修复中要求选用合理的熔铸金属,以保证修复部位的金属机械性能。在各部位激光修复后再进行金加工,然后对轴承配合部位进行耐磨层喷涂(钴基镍铬合金)。恢复到受损前的原始尺寸。修复后对转子作动平衡检验,剩余不平衡量左为10.05克、右为6.107克,检验合格(合格值为小于50克)。
5月12日处理完装配试车各振动数据见表3,罗茨鼓风机振动大大降低,确保了设备安全正常运行。
4结论
4.1设备故障诊断技术是提高设备检修质量和效率的有效手段。
4.2诊断测点及方向的选定对提高诊断的准确性有举足轻重的作用,监测测点应尽量地反映机器可能出现的各类故障信息。
4.3机械设备振动故障形式多种多样,各不相同,原因是复杂和交错影响的,振动故障源也可能是多源头的,所以应综合采用多种监测技术和手段。
4.4激光熔覆新技术加表面喷镀对大型风机轴修复经济、实用、可靠。
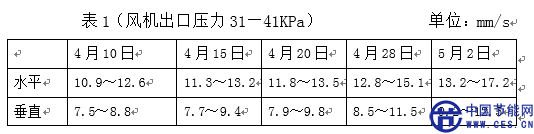
引起罗茨鼓风机振动大的因素较多,主要原因有以下几种:
1.1地脚螺栓松动,主要表现在垂直方向振动较大。
1.2联轴器找正不合格,表现有三点:一是轴向振动较大,二是与联轴器靠近的轴承振动较大,三是振动程度与负荷关系较大。
1.3风机基础刚度差,故障特征为:一是振动频率为工频,振动时域波形为正弦波,二是垂直方向振动速度异常。
1.4与风机连接的管道配置不合理,主要是与风机连接的防振接头老化,管道与风机形成共振。
1.5同步齿轮啮合间隙大,齿面接触精度不够,也可导致水平振动超标。
1.6转子不平衡,振动表现为:一是水平方向振动较大,且振动频率与转速同频,二是振动大小与机组负荷无关。
1.7轴承损坏及轴系零件松动,主要表现在:一是轴承温度高并有异响,二是水平、轴向、垂直振动都有异常。
2故障查找
对照以上分析情况,分别对风机地脚螺栓、联轴器、风机基础及与风机连接的管道进行了检查,未发现异常。并且在2007年因振动大对风机基础进行过重新加固浇灌,因此也可以排除风机基础刚度差的原因。轴承温度无变化以及未发现异常声音。
为查清原因,5月3日用振通908简易测振仪对风机水平、垂直、轴向振动进行测量,风机出口压力在31—41KPa运行时结果如表2,由测量结果可看出,后轴承端比前轴承端振动值大3mm/s左右,说明振动是从后轴承端引起。为检查是否存在转子动不平衡,对风机出口压力下降到21--34KPa和升到35—45KPa分别进行了测量,振动值无明显变化。因此可以肯定,风机转子不存在动不平衡,振动源出在风机后端,可能是轴承及轴系零件松动造成。
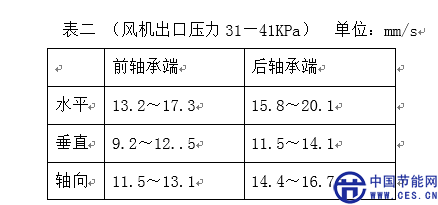
3故障处理
ARG500罗茨鼓风机叶轮与轴采用热装,无法更换轴,而购买一套转子费用较高,时间较长,是生产经营所不允许的。经分析研究决定对轴进行修复,为防止转子产生弯曲变形,以及表面粗糙度达到要求,采用激光熔覆新技术和表面喷镀方法。
3.1激光熔覆技术的原理及特点
激光熔覆,通常采用预置涂层或喷吹送粉的方法加入熔铸金属,利用激光束聚焦能量极高的特点,在瞬间将基体表面仅微熔。同时使基体表面预置的熔覆层金属粉末(与基体材料相同或相近)全部熔化。当激光离出后快速凝固,获得与基体冶金结合的致密覆层。从而达到使零件表面恢复几何尺寸和表面涂层强化的作用。
激光熔覆技术可以解决手工电弧焊、氩弧焊、喷涂、镀层等传统修复方法无法解决的材料选用局限性、工艺过程热应力、热变形、材料晶粒粗大、基体材料结合强度难以保证等问题。激光熔覆层与基体为冶金结合,结合强度不低于原基体材料的90%,基体材料在激光加工过程中仅表面微熔,微熔层为0.05~0.1mm,基体热影响区一般为0.1~0.2mm,温升不超过80℃,激光加工后无热变形。且覆层组织致密,晶体小、无孔洞、无夹渣裂纹等缺陷。
3.2修复过程
修复工作委托昆钢联合激光公司进行,利用一台2KW的激光机,对所需修复部位进行手工熔覆修复。在修复中要求选用合理的熔铸金属,以保证修复部位的金属机械性能。在各部位激光修复后再进行金加工,然后对轴承配合部位进行耐磨层喷涂(钴基镍铬合金)。恢复到受损前的原始尺寸。修复后对转子作动平衡检验,剩余不平衡量左为10.05克、右为6.107克,检验合格(合格值为小于50克)。
5月12日处理完装配试车各振动数据见表3,罗茨鼓风机振动大大降低,确保了设备安全正常运行。
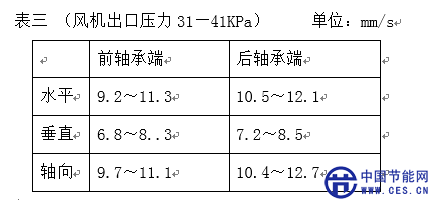
4.1设备故障诊断技术是提高设备检修质量和效率的有效手段。
4.2诊断测点及方向的选定对提高诊断的准确性有举足轻重的作用,监测测点应尽量地反映机器可能出现的各类故障信息。
4.3机械设备振动故障形式多种多样,各不相同,原因是复杂和交错影响的,振动故障源也可能是多源头的,所以应综合采用多种监测技术和手段。
4.4激光熔覆新技术加表面喷镀对大型风机轴修复经济、实用、可靠。