1 改进VOCs催化燃烧装备的原因
挥发性有机物(Volatile Organic Compounds, 简称VOCs),是国家大气污染控制的重要对象,近几年针对VOCs排放出台多项环保标准。国内工业VOCs净化行业目前处于渐热状态,在有机挥发性废气催化燃烧装备中,多数环保企业采用蓄热式催化燃烧装置,该技术方法采取两室、三室及以上的蓄热催化燃烧器,使VOCs 气体发生催化氧化反应,产生的热量存储于蓄热载体中,通过频繁切换阀体(切变气体流动管路),达到冷、热流体热量交换的目的。
蓄热式催化燃烧装备可以实现自给供热,具有比较好的应用效果。然而,装备本身存在着运行操作不能完全连续化、设备制造成本较高、装备使用时占用体积较大、安装调试中对电气控制要求较高等缺点,对此,需要设计一种操作简单、可实现连续化运作、高效低成本的一体化VOCs废气净化装备。
2 改进后的VOCs连续催化燃烧装备
本公司结合生产、施工的相关经验,对过程装备进行改进,改进后的装备简图如图1 所示。结构中包括以下几个部分:①有机废气进口管、出口管;②废气进口浓度检测控制器、催化剂床层进口温度检测控制器;③废气换热器、电加热棒、处理器上盖板、气流隔板;④催化剂床层、催化剂支撑板。
改进后的催化燃烧器可以进行连续化操作,有机废气进(冷气)和出口(热气)均经过废气换热器的进出端,冷侧流体与热侧流体在换热器中进行连续热交换,利用热量传递性质,热流体的热量经过壁传热、对流传热过程传递至冷流体中;废气换热器的冷侧出口气,经过电加热棒区域,对含VOCs废气进行加热升温;经加热的废气顺着压力梯度会越过气流隔板进入催化剂床层,废气在VOCs催化剂表面发生催化氧化作用,可以实现在较低温度下废气催化燃烧,放出氧化反应热。气流顺着催化剂宏观孔道流动,经支撑板后进入废气换热器,与冷流体间接接触换热,从废气换热器的热侧出口流出,继而完成最终排放。
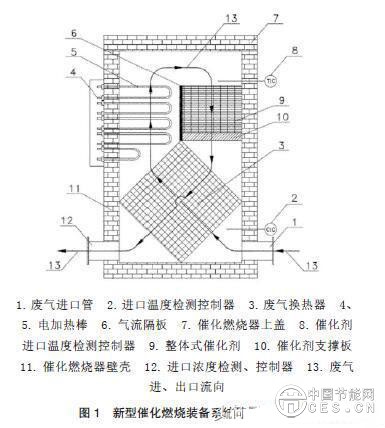
3 新型VOCs连续催化燃烧装备技术浅析
3.1 废气热交换器技术分析
废气热交换器的结构设计是装置的首要关键点,直接影响着装备运行的稳定性和处理效率。在设计和安装调试中需要考虑到以下几个因素。
(1)气体流动情况与运行成本。气体流动湍流程度越高,换热效率就越高。湍流程度增加,意味着操作费用上也会随之增加。在设计过程中既要考虑到运行效果,也要考虑设备制造成本和操作费用,因此需要对换热器流体状态方面进行优化。
(2)换热器内部结构与材料的选择。换热器管壁两侧均为气相流体,前后进出口气量基本接近,根据换热器传热计算公式,为了增加热交换效率,需要提高两侧气体的传热系数。在实际应用中,在热交换管内外安装耐温翅热片,换热效果会明显增加。另外热交换进出口两侧分别为高、低温,气体温差较大,对材料抗热应力性能要求较高,因此生产制造中需要采用抗热应力材料。
(3)换热器的布置与运行的稳定性。对于换热器的整体布置,一般情况下,立式或者卧式布置。本设计中为节省装备的占用面积,热交换器采用相对水平方向45 度排布。但应注意的是,进、出气流会对换热器管壁产生冲卸力,两种冲卸力对换热器共同作用,形成扭矩,极大的影响了换热器的稳定运行,因此需要对换热器四角和侧壁进行牢固焊接。
(4)密封性。进口气体中含一定浓度的VOCs,出口气体中基本不含有VOCs,热交换器不进行密封处理,会出现“串气”现象,导致设备出口气体不能达到排放标准。对此,将换热器冷端进口处与换热器气体进口之间、热端出口与装备出口之间用金属直角挡板进行密封焊接。
3.2 电加热器区域结构技术分析
电加热器结构的设计会影响后续的催化燃烧工序,是该装置设计的第二关键点。气体经加热后进入催化剂床层时,对气体流动和温度要求较高,具体如下:其一,气体温度需均匀,若温度存在差异,经加热的气体进入催化床层反应后,导致催化床层温度出现不均匀。催化氧化反应属于放热反应,继而更容易出现床层温度超出设计温度的情况,影响催化剂的寿命。其二,气体流动尽量均匀,对于催化剂,最理想的情况是每个催化剂活性位都能与VOCs 分子同一停留时间接触反应。若流动状态不均匀,VOCs 分子停留时间上会出现差异,继而会影响到催化剂的使用效率和使用成本。
本方案中加热区域位于热交换器、隔离板之间,形成“梯形”结构,换热器出口气流会与器壁存在碰撞,会损失部分能量,气体流动也不均匀,对此保证气体能够均一流通、均匀加热是设计中必须要考虑到的。
为了达到以上目的,本方案在“梯形”区域下部加热区域要求加热功率要低并设置非均一孔金属网,靠近设备壁处设置小孔(孔径接近整体式催化剂孔径),目的是增加部分阻力,抵挡住拐角气流的冲力,均匀气流。在靠近挡板处网孔设置大孔,方便气流的正常通过。另外在加热棒之间参插大孔径的金属网块,一方面加热棒表面会产生高温热辐射,辐射至金属网块表面,加速了金属网块的加热过程,除此之外,金属网块会进行快速热传导,扩大了加热范围,提高了气- 固传热接触面积。但在实际制造中还需要对加热棒和网块之间进行绝缘处理,或者在加热棒外部套入隔网,防止触碰导电。经过试验测试,在气量3000m3/h,气体出口温度测量截面点温度相差5%,整体加热区域气体阻力大约30~50Pa,气流均匀性较好。
3.3 催化燃烧催化剂技术分析
对于气流在催化剂中的相关状态和要求,在上述(二)中已部分介绍。除前述外,对催化剂设计和改造上还需要考虑以下重要的环节。
(1)处理废气量应减少。废气量增大,若要达到规定去除率,在催化剂去除能力不变的情况下,需要增加催化剂的用量,但目前市场来看,效果较好的催化燃烧催化剂单价(元/m3)均在十几万元,会增加设备的成本。在实际操作中,可以先对废气的VOCs进行浓缩预处理(浓缩操作需要低于爆炸极限),再通过脱附操作将VOCs 脱附出来(脱附浓度也需要低于爆炸极限),以降低装置的使用投资成本和操作。
(2)在催化剂用量计算上,需要综合考虑到催化剂的类型、VOCs的组成、反应温度等因素,不能只参照某一因素考虑。
(3)催化剂选择应严谨。比如催化剂对含卤素气体要求较高,需优先对该种废气进行预处理,然而这样会大大增加处理成本,因此要在工艺优化、成本综合计算之后才能确定催化剂。对于可能会导致催化剂中毒的物质,需要对中毒物质进行预先去除。
(4)催化剂使用过程中,需要保持表面洁净,即定期对催化剂进行清洗工作。可以采用压缩空气、过热蒸汽、洗涤剂等方式进行清洗。对于废气中含有少量的有机颗粒,在低于设计温度下运行操作时,不完全燃烧易导致催化剂表面结碳,堵塞催化剂活性位,降低了催化剂使用效率,此时通入高温蒸汽可以通过重整反应,去除积碳,可以还原催化剂的活性。
(5)在催化剂材质上,最好选用导热性能高的材料,比如整体式催化剂采用铝金属基(如图2 所示),由于铝金属材料本身导热性能高,加热后的气体经过金属催化剂床层,催化剂活性组分可以迅速被起燃,催化效率很高。经测试,在装置实际调试运行期间,催化剂被起燃的时间可以缩短50%~60%(与堇青石整体式蜂窝催化剂进行对比),另外金属材质蓄热能力低,这样催化剂出口气体的温度会得到一定的提升,在一定的程度上热量可以得到更好的回收利用。
(6)催化剂的装填也会对气体的流动分布和催化剂床层温度分布产生影响。在装填中需要考虑到催化剂的密实性,装填中要求均匀装填,紧密一致,无空隙,催化剂床层边壁保温。在整体式催化剂层与层间以及催化剂床层边缘处可以适当的添入多孔耐高温绵,既可以避免由于层间孔道的错位、边缘空隙导致的气流上的不均匀性和壁效应导致的气体沟流、短流等现象,同时边壁添入耐高温绵之后会对设备起到一定的保温效果。另外整体催化剂装填前需要检测,检测结果上需要符合相关检测标准。
蜂窝孔道截面形状、孔径、孔密度等参数的设计也很重要,这关系到气阻,气流均布性、气体的停留时间、转化效率等重要参数。孔径选择越小,气阻越大,停留时间越短,转化效率较低,但废气处理量大。
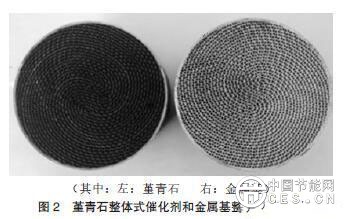
4 结语
综上所述,改造后的连续催化燃烧器与传统的蓄热RCO 相比,具有占地面积小、运行连续、电控要求低等优点。由于设备详细结构较多,本文中从流体动力学工程、催化工程、传热工程等多角度,对重要的废热交换器、加热结构、催化燃烧催化剂技术进行浅层的分析。可以看出,在细节设计上,都需要对过程因素进行优化,既要考虑到设备的高效运行,又要考虑到制造企业的生产成本和被实施企业方实际的运行成本。在技术快速发展的今天,我们可以利用现代计算机技术进行辅助模拟设计优化设备参数,在一定程度上可以节省时间,提升优化效果。
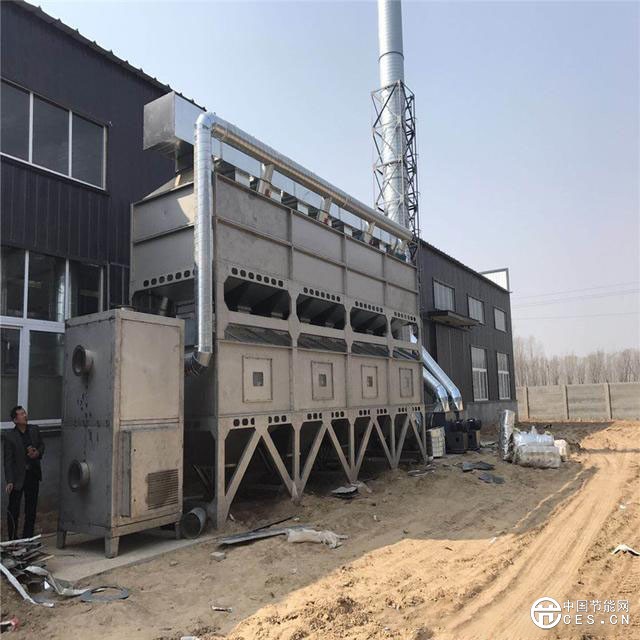
蓄热式催化燃烧设备RCO